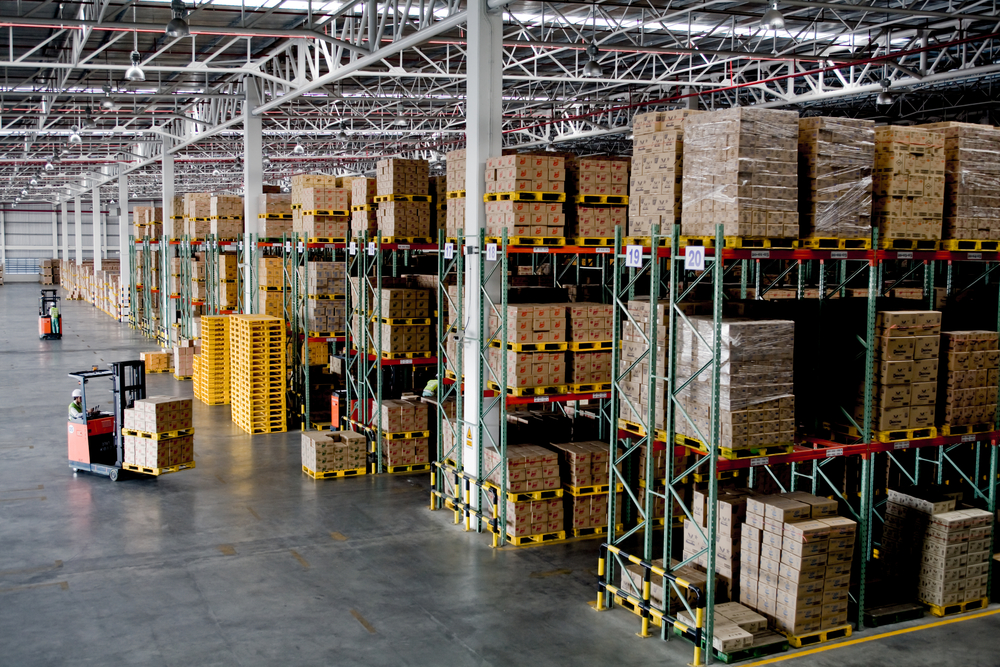
Understanding the Amazon Fulfillment Center
An Amazon fulfillment center is a massive, high-tech warehouse where millions of products are stored, sorted, packed, and shipped to customers worldwide. These fulfilment centers operate with a combination of automation and human efficiency, ensuring that orders are processed quickly and accurately. With thousands of employees working in shifts alongside advanced robotics, Amazon has built a fulfillment network that minimizes delays and maximizes customer satisfaction.
The Daily Operations of an Amazon Fulfillment Center
Inbound Shipments: Receiving and Storing Inventory
Every day, truckloads of goods arrive at Amazon fulfillment centers, bringing in inventory from suppliers and third-party sellers. The receiving process starts with workers unloading shipments and scanning each item into Amazon’s tracking system. Once scanned, the items are placed into storage bins or shelving units, ready for fulfillment when orders come in. Unlike traditional warehouses, where products are stored in specific categories, Amazon’s fulfilment centers use a chaotic storage system. This method relies on barcode scanning and algorithms to determine the most efficient placement of items, reducing retrieval times.
Picking: Locating and Retrieving Ordered Items
When a customer places an order, Amazon’s system instantly assigns it to a picker. The picker, equipped with a handheld scanner or wearable technology, is guided to the exact location of the items needed. Fulfillment centers are massive, often spanning over a million square feet, so employees rely on automated systems to optimize their walking paths, ensuring the fastest route to collect products. Some facilities also use robotic shelves that move toward pickers, further streamlining the process.
Sorting: Organizing Orders for Accuracy
After items are picked, they move to sorting stations, where they are grouped based on the destination and shipping method. This step ensures that orders containing multiple items are packaged together, reducing unnecessary shipments. Employees verify product accuracy before items move to the next phase to prevent errors in customer deliveries.
Packing: Preparing Orders for Shipment
Amazon’s packaging process is designed to be both cost-effective and environmentally friendly. The system determines the ideal box size for each order, minimizing wasted space and reducing shipping costs. Automated machines apply the correct amount of packing material, seal the boxes, and print shipping labels. At high-speed fulfilment centers, advanced robots assist in boxing items, significantly speeding up the process.
Outbound Shipping: Delivering Orders to Customers
Once packed, orders are sent to outbound docks, where they are sorted by destination. Some packages go directly to delivery partners like UPS, FedEx, or Amazon’s own fleet of delivery vans, while others are sent to regional distribution centers for further processing. Amazon’s fulfilment network is designed for speed, meaning many orders qualify for same-day or next-day delivery.
Advanced Technologies Driving Amazon Fulfillment Centers
Robotics and Automation in Fulfillment
Amazon’s use of automation has transformed the way fulfilment centers operate. Robotic arms, conveyor belts, and AI-driven software handle tasks with extreme precision. Autonomous robots transport inventory, eliminating the need for employees to walk long distances. Machine learning algorithms predict demand patterns, optimizing inventory levels and reducing waste.
Artificial Intelligence for Order Optimization
AI plays a crucial role in ensuring orders are processed with maximum efficiency. The system continuously analyzes real-time data to adjust fulfillment strategies, rerouting shipments when needed and prioritizing high-demand products. AI also helps Amazon reduce operational costs by predicting peak shopping periods and adjusting labor allocation accordingly.
Key Factors to Remember About Amazon Fulfillment Centers
Fast-Paced Work Environment
Employees in Amazon fulfillment centers work in a highly structured, fast-paced setting. Productivity targets are set for every task, from picking to packing, ensuring that orders meet strict shipping deadlines. Workers rotate between different roles to maintain efficiency and reduce fatigue.
Stringent Quality Control Measures
Amazon has a zero-error policy when it comes to order accuracy. Multiple checkpoints throughout the process ensure that customers receive the correct items in pristine condition. Automated scanning systems detect defects, damaged products, or incorrect labels before shipments leave the facility.
Scalability for Seasonal Surges
During peak seasons like Black Friday and the holiday shopping rush, fulfilment centers ramp up operations by hiring temporary workers and increasing automation capacity. The ability to scale operations ensures that Amazon can handle millions of orders without delays.
Sustainability Initiatives
Amazon has implemented several eco-friendly practices within its fulfillment centers. From reducing packaging waste to investing in renewable energy, the company aims to minimize its carbon footprint while maintaining rapid delivery speeds. Robotics also play a role in sustainability by improving efficiency and reducing unnecessary transportation.
Final Thoughts on Amazon Fulfillment Centers
Amazon’s fulfilment centers operate with unmatched precision, leveraging technology and human expertise to process millions of orders daily. From receiving inventory to final shipment, every step is optimized for speed and accuracy. As e-commerce demand continues to grow, Amazon’s fulfillment network will only become more sophisticated, setting the benchmark for modern logistics.